Mastering Liquid Control: The Importance of Level Gauges in Industrial Applications
Industries that involve the handling of liquids require precision and control in their operations. An integral component that plays a vital role in the monitoring and managing of these liquids is the level gauge. This device, although often understated in the day-to-day functions of a facility, is essential for ensuring safety, efficiency, and the smooth running of numerous industrial processes.
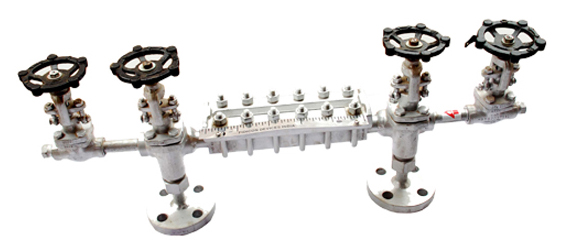
Understanding Level Gauges and Their Function
A level gauge is an instrument used to measure the level of a liquid within a container or in natural forms like ponds or tanks. Its usage spans a wide range of industries including chemical, pharmaceutical, oil and gas, food and beverage, and water treatment, amongst others. The need for precise liquid measurement is not only a question of operational efficacy but is also crucial for maintaining industry standards and ensuring worker safety.
Level gauges come in various types and designs, each suited to specific conditions and purposes. From simple mechanical float-operated devices to sophisticated electronic gadgets that provide digital readings, the technological evolution of this tool has expanded its capabilities and accuracy.
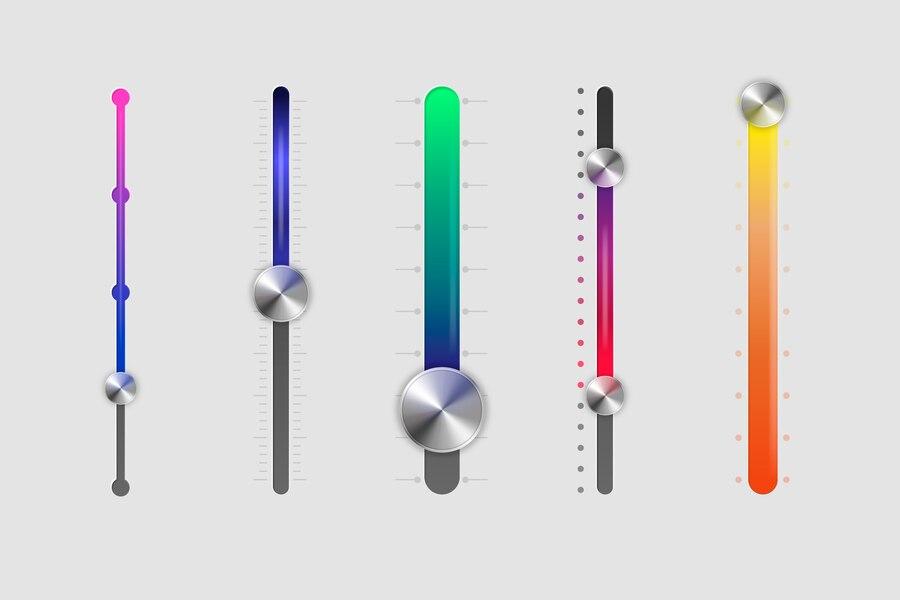
Operational Safety and Level Gauges
One of the primary reasons for the imperativeness of level gauges in industrial environments is operational safety. Hazardous materials, such as volatile chemicals or hot liquids, require careful monitoring to prevent overflows or leaks, which can lead to accidents, equipment damage, and potentially catastrophic environmental impacts. Level gauges help to mitigate these risks by providing real-time updates on liquid levels, enabling prompt and informed decisions.
Efficiency and Cost Savings
Efficiency in production is paramount for any industry. A high-quality level gauge can serve as a control mechanism, ensuring that processes that depend on precise liquid volumes are carried out without interruptions. Avoiding the wastage of materials and time is key to maximising profits, and having an accurate reading of liquid quantities can significantly reduce the probability of errors and the associated costs of rectification.
Compliance with Industry Standards
Regulatory compliance is another aspect where level gauges play an essential role. Many industries are governed by strict guidelines on how liquids are to be stored and handled. Having accurate level measurements is part of meeting these standards, with data often being essential for audits and quality assurance documentation. Inaccurate readings can lead to violations, fines, or worse, to legal and financial liabilities stemming from accidents.
Environmental Considerations
In today’s context, industries are increasingly held accountable for their environmental footprint. Spillages due to improper liquid monitoring can have severe repercussions on the local ecosystem. Employing reliable level gauges not only helps in preventing such incidents but also highlights an organisation’s commitment towards environmental conservation.
Real-time Data and Process Optimisation
The integration of advanced level gauges into industrial systems has paved the way for real-time monitoring and analytics. Facility managers can now take advantage of the data provided to optimise processes, enhance predictive maintenance, and minimise downtime. The continuous feedback from level gauges facilitates better decision-making and seamless production workflows.
Moreover, with advancements in connectivity, such as Internet of Things (IoT) devices, level gauges can be linked to centralised networks that allow for remote monitoring and control. This digital integration represents a move towards smarter, more responsive industrial operations.
Selection Considerations for Level Gauges
Selecting the appropriate level gauge for a particular industry or application is crucial. Factors to consider include the type of liquid (corrosive, non-corrosive, viscous, etc.), operating conditions (pressure, temperature), container size and shape, and whether the environment is hazardous. It is also important to evaluate the accuracy required, the method of readout (local or remote), and the ease of installation and maintenance.
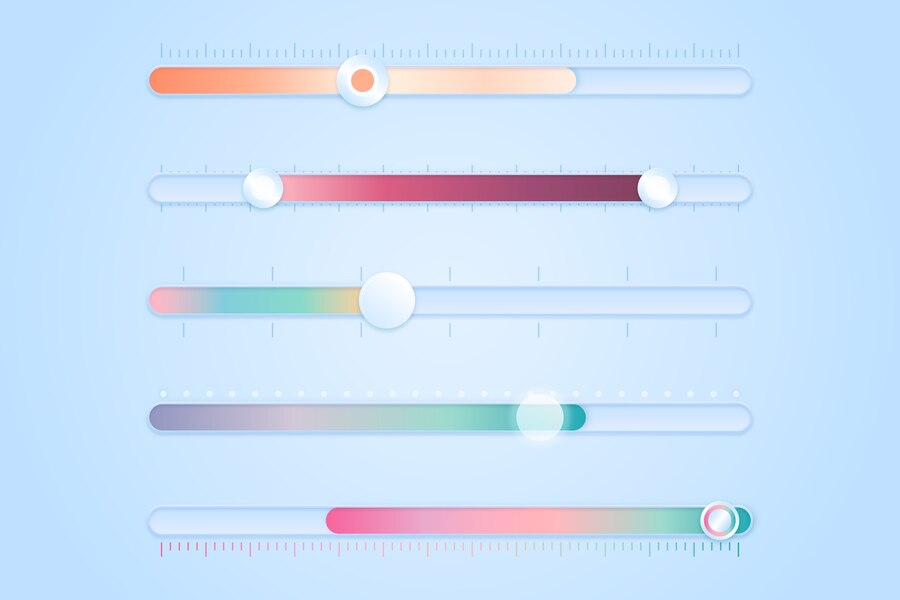
Technological Advancements in Level Gauges
The technological advancements in level gauge design and function have been significant. Cutting-edge sensors now provide precise measurements under extreme conditions and are built to withstand the rigours of industrial use. Furthermore, with the advent of digital readouts, the margin for human error in interpreting levels has been greatly reduced.
Maintaining Level Gauges for Lasting Performance
To ensure their continued effectiveness, level gauges must be properly maintained. This may involve routine cleaning, calibration, and inspection for wear and tear. Maintenance practices and schedules can often be found in the manufacturer’s documentation, or by directly consulting with experts who specialise in fluid measurement and control systems.
Custom Solutions and Consultation
Companies may on occasion require customised level gauge solutions to meet specific needs. In such cases, working with reputable suppliers who can provide tailor-made instruments and professional consultation is advisable. It is also beneficial to engage with suppliers who offer comprehensive post-sale services, including technical support and training.
Conclusion
In conclusion, level gauges are indispensable instruments in the realm of industrial fluid handling and measurement. Their role extends well beyond mere monitoring; they contribute significantly to safety, efficiency, regulatory compliance, and environmental responsibility. With the right level gauge in place, industries can achieve greater control over their liquid assets, reducing risk and enhancing the overall effectiveness of their operations.
For facilities looking to maintain precise control over their fluid processes, choosing a high-quality, reliable level gauge from a trusted supplier is a decision that will have a lasting impact on their production capabilities and success.
In the dynamic world of industrial applications, mastery over liquid control is not just a technical requirement; it is a strategic advantage that can very well define excellence in operation and sustainability in practice.
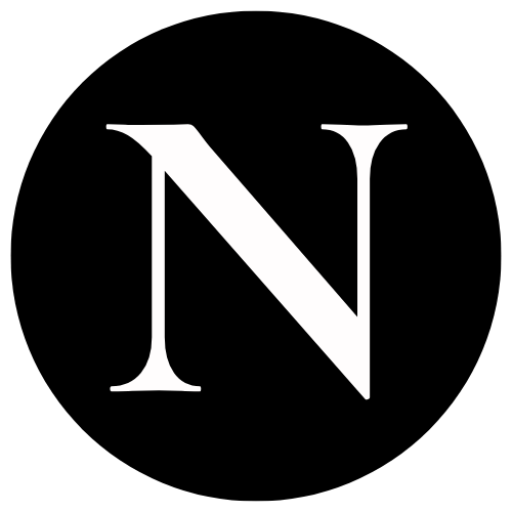